quality compliance consulting
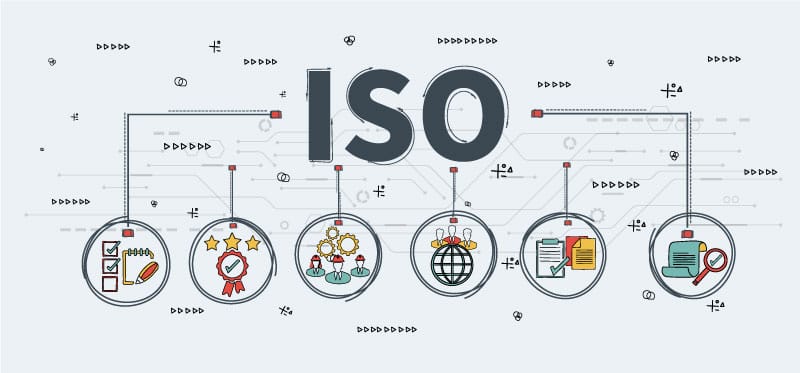
One of the biggest challenges that companies face when trying to establish a quality management system (QMS) that complies with ISO standards is the complexity and resources required for implementation. Some specific challenges include:
- Understanding the Requirements: ISO standards are detailed and can be complex, requiring a deep understanding of their specific requirements.
- Resource Allocation: Implementing a QMS requires dedicated resources. They include time, money, and personnel, which can strain smaller organizations, those with limited budgets, or those that lack time or expertise.
- Integration with Existing Processes: Aligning existing processes with ISO standards can be challenging, especially if there are conflicting or outdated practices that need to be revised.
- Training and Awareness: Ensuring that employees are aware of and trained in the requirements of ISO standards is crucial and can be time-consuming and costly.
- Documentation and Record Keeping: ISO standards require extensive documentation and record keeping, which can be overwhelming for organizations without established systems in place.
- Audits and Certification: Achieving and maintaining ISO certification requires regular audits, which can be rigorous and require significant preparation and coordination prior to annual registrar visits.
- Continuous Improvement: ISO standards emphasize continuous improvement. This require organizations to regularly review and update their QMS, a process that can be a challenge to sustain over time.
Outsourcing the establishment of a Quality Management System (QMS) to EMDS can be a major benefit if your company wishes to streamline its operations and reduce costs. You can leverage the expertise of our specializations to ensure the system is set up efficiently and ensures continued maintenance moving forward. You’ll stay compliant with ISO standards and focus on your core business activities, while we manage the complexities of maintaining your QMS.
QMS DEVELOPMENT
The initial stage of Quality Management System (QMS) development involves several key steps in which EMDS has considerable expertise:
- Define the scope and objectives of the QMS by identifying the processes and areas of your organization that will be covered by the system.
- Conduct a gap analysis to assess the current state of your organization’s quality management practices against the requirements of relevant standards, such as ISO 9001.
- Based on this analysis, develop a roadmap that outlines the steps needed to implement the QMS, including the allocation of resources and timelines.
- Coordinate a project team to oversee the implementation process, ensuring that all stakeholders are engaged and that the QMS is tailored to the specific needs of your organization.
QMS documentation
EMDS offers expertise in development of the QMS documentation stage, critical for ensuring that all processes, procedures, and policies are clearly defined and documented in accordance with ISO standards. This involves:
- Creating the necessary documentation to support the implementation and maintenance of the QMS, such as quality manuals, procedures, work instructions, and forms.
- Ensuring documentation is comprehensive, yet concise and easy to understand and can be effectively implemented and followed by all employees.
- Establishing a document control system to manage and maintain all QMS-related documents, ensuring that they are up-to-date and accessible by authorized personnel.
QMS maintenance & monitoring
You can trust EMDS to effectively implement the maintenance and monitoring stage of Quality Management System (QMS) development at our business. Several key components ensure the effectiveness of the QMS:
- Internal auditor programs are established to conduct regular audits of the QMS, verifying continued compliance with standards and identifying areas for improvement.
- Corrective action systems are implemented to address nonconformities identified during audits or through other means, ensuring that issues are resolved and do not recur.
- Preventive action systems are also put in place to proactively identify and mitigate potential risks to the QMS, helping to prevent issues from arising.
- Calibration systems are established to ensure that all measuring and monitoring devices used in the QMS are accurate and reliable, providing confidence in the integrity of the QMS and its processes.
AREAS OF INDUSTRY EXPERTISE IN QUALITY COMPLIANCE
Your business is in good hands with our quality compliance consulting, targeted for the following industries:
AUTOMOTIVE
In the automotive industry, a QMS is critical to ensure the production of safe, reliable, and high-quality vehicles. These systems help automobile and auto parts manufacturers adhere to stringent quality standards and regulatory requirements, such as ISO/TS 16949, which is specific to the automotive sector. QMS in the automotive industry also focuses on continuous improvement, waste reduction, and customer satisfaction to drive competitiveness and meet evolving market demands.FOOD MANUFACTURING
In the food manufacturing industry, a QMS is essential to ensure the safety and quality of food products. These systems help manufacturers comply with food safety regulations, such as HACCP (Hazard Analysis and Critical Control Points), to identify and control food safety hazards. QMS in the food industry also focus on maintaining hygiene standards, traceability of ingredients, and meeting customer expectations for safe and high-quality food products.FOOD SERVICE
In the food service industry, QMS’s play a crucial role in ensuring food safety, customer satisfaction, and operational efficiency. The systems help establishments comply with food safety regulations, such as those set by the FDA or local health authorities, by implementing practices like proper food handling and storage. QMS in the food service industry also focus on maintaining consistent service quality, managing inventory effectively, and ensuring a clean and safe environment for customers and employees.PHARMACEUTICALS
In the pharmaceutical industry, QMS’s are vital for ensuring the safety, efficacy, and compliance of pharmaceutical products. They help manufacturers adhere to strict regulations, such as Good Manufacturing Practices (GMP), to maintain product quality and safety. Finally, the focus on documentation, risk management, and continuous improvement to meet regulatory requirements and deliver high-quality medicines to patients.
CHEMICAL MANUFACTURING
In the chemical manufacturing industry, QMS systems are crucial for ensuring the safety, quality, and compliance of chemical products. They help manufacturers adhere to regulations such as REACH (Registration, Evaluation, Authorization, and Restriction of Chemicals) and ensure that their products meet stringent quality standards. QMS in the chemical industry also focus on risk management, process optimization, and continuous improvement to enhance product quality and maintain a safe working environment.
MEDICAL EQUIPMENT
In the medical equipment industry, Quality Management Systems are essential to ensure the safety, reliability, and effectiveness of medical devices. The QMS systems help manufacturers comply with regulations such as ISO 13485, which sets quality management standards specific to medical devices. QMS in the medical equipment industry also focus on risk management, traceability, and documentation to ensure that products meet regulatory requirements and customer expectations.
OFFICE FURNITURE
In the office furniture industry, QMS systems are important to ensure the durability, safety, and ergonomics of office furniture products. These systems help manufacturers adhere to quality standards and regulations, such as ANSI and/or BIFMA, which define safety and performance requirements for office furniture. QMS in the office furniture industry also focus on design consistency, material sourcing, and customer satisfaction to deliver high-quality products that meet the needs of modern office environments.
RAIL
In the rail industry, QMS systems are important to ensure quality at each step of the supply chain in the production of rail machinery. These systems help manufacturers adhere to quality standards and regulations, such as ISO/TS 22163, which increase the focus on project and safety management in the rail sector. Rail production is viewed like project management, as no two rail producers build identical units. Because of this, there is a firm focus on quality, safety, design, material sourcing, and customer satisfaction to deliver high-quality units that meet the needs of each type of train. If your business is in need of additional QMS resources, and if you’re serious about a quality system that meets standards and passes audits, connect with our team to find out more information. We not only blend with your team, but energize it so you maintain a QMS edge over your competitors.
OSHA Supported Standards
Include but are not limited to: